Argon wire is an essential component in welding, and it requires careful consideration when selecting the appropriate wire type and size for specific welding tasks. One of the most popular wires used in welding is the copper-plated non-alloy cored wire for welding in CO2 and the atmosphere suitable for joints on Non-alloyed steels, for storage tank construction and for pipes welding with a high tensile strength. This type of wire is not only compatible with CO2 but also with Argon mixtures, making it ideal for various welding applications.
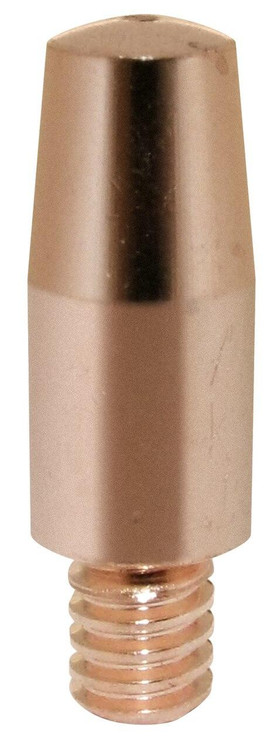
Argon is an excellent option for welding as it provides various benefits, including high-quality results, easy handling, and less fumes. Argon, being an inert gas, can provide superior welds with a minimal amount of distortion and cleaner-looking welds with fewer defects.
When combined with the appropriate Argon wire, welders can expect a higher quality finish, better penetration, and fewer spatters. Furthermore, Argon-based welding wires tend to offer more significant benefits concerning the welding process and the finished product.
Welding is one of the most challenging industrial processes that requires the highest level of skill and knowledge to execute efficiently. Argon wire has been developed by companies like Jiangsu Jinqiao Welding Materials Technology Co., Ltd to make welding easier and much more manageable.
This company has developed welding wires that are compatible with a wide range of alloys, including non-alloy steels, making it very versatile. With this technology, it is possible to weld a broad range of steels without sacrificing the quality of the finished product.
Argon wire is an excellent option when welding high-strength steels, as it has excellent penetration capabilities. This wire can create highly consistent and evenly distributed welds, which is critical when welding high-strength materials that require particular attention.
Furthermore, Argon wire offers the advantage of less fumes during the welding process, making it safer and more environmentally friendly. Welding produces smoke and fumes that can be hazardous to human health and the environment. The combination of Argon and copper-coated non-alloy cored wire reduces the amount of smoke and fumes produced during the welding process, making it safer for workers.
Another benefit of Argon wire is that it requires lower heat input to produce the same results as other welding methods. This means that welders can reduce their overall energy costs and improve their efficiency by using Argon wire.
In conclusion, Argon wire is a highly beneficial component in welding that offers many advantages to both experienced and novice welders. Choosing the appropriate wire size and wire type is critical, and combining Argon gas with appropriate wire type can create highly consistent and evenly distributed welds. The combined use of Argon gas with the copper-coated non-alloy cored wire reduces fumes, produces fewer spatters, and results in high-quality welds that are much safer for the operator and the environment. Welders can significantly improve their productivity and efficiency by using this type of welding smote and reduce their energy costs.