Stainless steel is a popular material for a variety of applications in industries ranging from aerospace to construction. It offers a combination of corrosion resistance, toughness, strength, and a good appearance that make it an ideal choice for many purposes. However, welding stainless steel can be challenging, and proper selection of filler metals is crucial to ensure that you get the most out of your welding applications.
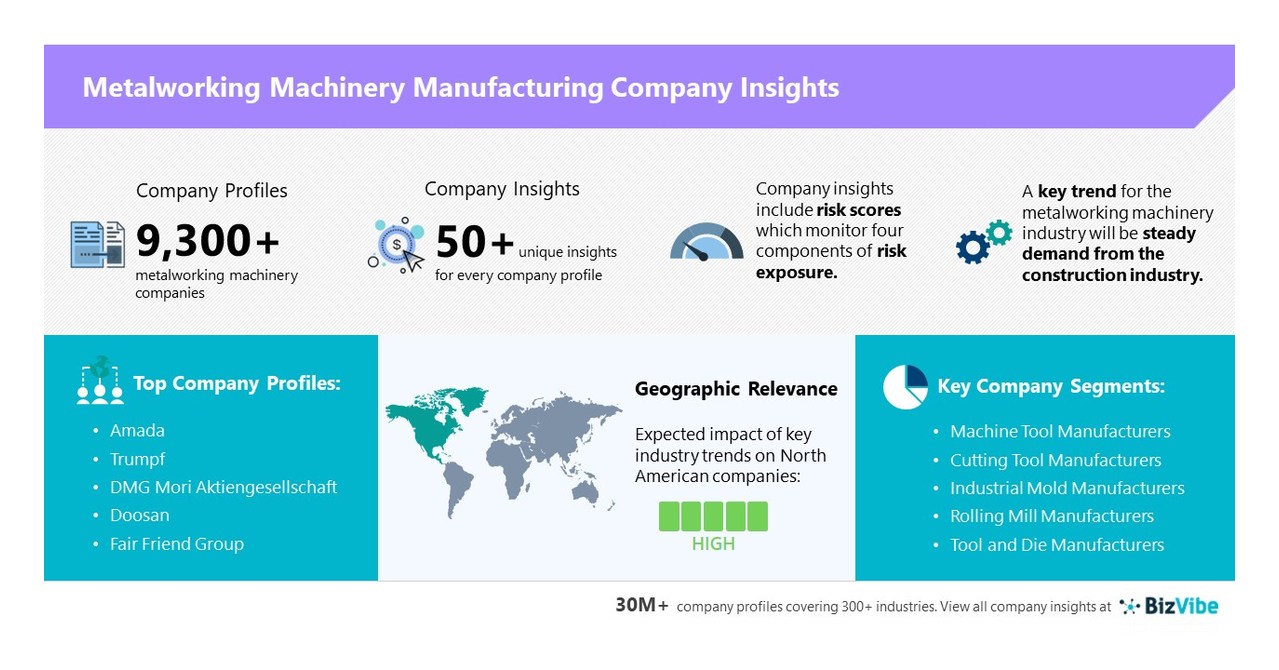
Filler metals are used to join two materials together in the welding process. They are typically made of the same material as the base metal but can also contain different alloys or materials to improve the properties of the weld. There are a few different options when it comes to selecting a filler metal for welding stainless steel, and choosing the right one can make all the difference in the quality and integrity of the weld.
One of the main challenges of welding stainless steel is its tendency to warp when exposed to heat. This is because stainless steel has a much higher thermal conductivity than other materials, so it can quickly transfer heat from the weld zone to surrounding areas, causing distortion and warping. To avoid this, it is essential to use the correct filler metal and welding techniques.
When selecting a filler metal for welding stainless steel, it is essential to consider the type of stainless steel being used, as well as the desired properties of the final weld. Some filler metals are designed for specific types of stainless steel, such as austenitic, ferritic, or duplex stainless steel, while others are more versatile and can be used with multiple types. In general, the filler metal should have similar or slightly higher levels of nickel, chromium, and molybdenum than the base metal to ensure good corrosion resistance and strength.
Another important consideration when selecting a filler metal for welding stainless steel is the welding process being used. Different processes, such as TIG, MIG, or stick welding, require different types of filler metals and techniques to achieve the desired results. For example, TIG welding typically requires a filler metal with a smaller diameter and lower melting point to produce precise, high-quality welds, while MIG welding may use a larger diameter filler wire for faster and more efficient welding.
Filler wire for carbon steel welding is another critical consideration when welding stainless steel. Carbon steel filler wire is typically not recommended for welding stainless steel because it does not provide the same corrosion resistance, strength, or toughness as stainless steel filler metal. Using carbon steel filler wire for welding stainless steel can result in poor-quality welds, reduced corrosion resistance, and potential failure of the weld.
In conclusion, welding stainless steel can be challenging, but proper filler metal selection and welding techniques can ensure excellent results. When selecting a filler metal for welding stainless steel, it is essential to consider the type of stainless steel being used, the desired properties of the final weld, and the welding process being used. Using the correct filler metal can help prevent warping, ensure good corrosion resistance and strength, and produce high-quality welds that are durable and long-lasting. Always avoid using carbon steel filler wire for welding stainless steel, as this can result in poor-quality welds and potential failure of the weld.